Working principle of an alternator.
Principle of Operation
Fig. 14.14. Basic single-loop alternator.

In Fig. 14.14A the magnet rotates clockwise with its North Pole on the left-hand side and the South Pole on the right-hand side of the iron yoke. The lines of flux circulate round the yoke in a clockwise direction from the North to the South Pole. Also, the movement of the magnet causes the lines of flux to cut through the conductors and the induced voltage produces a flow of current in the conductor loop in a clockwise direction.
In Fig. 14.14B the magnet is now rotated a further half revolution so that the position of the magnet poles is reversed, with the North Pole being on the right-hand side of the yoke and the South Pole on the left-hand side. As a result, the direction of the lines of flux round the yoke is in an anticlockwise direction. This reverses the direction of flow of the generated current in an anticlockwise direction.
Thus due to the rotation of the magnet, the yoke poles continually change their north and south polarities. Consequently, the direction of the flux-path lines is constantly reversed so that the current in the conductors continuously changes from a maximum value in one direction to a maximum value in the opposite direction. A current with repeatedly changing of its direction of flow is termed as an alternating current (AC). With a two pole magnet the change of its
direction takes place once in every complete revolution of the magnet. The output produced by one complete revolution is called as an alternating-current cycle. 14.8.2. Construction
The alternators in practice use many conductor windings around a ring shaped yoke, known as the stator windings and the stator yoke (Fig. 14.15A). Also the rotor is made in two halves to reduce the voltage fluctuation further, and each half has several segment poles of like polarity so that when they are fitted together they form a ring of alternating North and South Poles (Fig. 14.15B).
Fig. 14.15. Alternator. A. Section view. B. Pictorial view of rotor and stator.
An exploded view of a typical alternator (Lucas) is shown in Fig. 14.16. This alternator is a 3-phase, 12 pole machine having a rectifier and micro-electronic regulator. The casing of the alternator is made of lightweight aluminium alloy, and it contains :
(i) the rotor to form the magnetic poles,
(ii) the stator to carry the windings in which the current in generated, (Hi) the rectifier pack to convert AC and DC, and
(iv) the regulator to limit the output voltage.
Fig. 14.16. Exploded view of alternato
Rotor.

The rotor has a field winding, wound around an iron core and pressed on to a shaft. An iron claw is placed at each end of the core to form 12 magnetic poles. Each claw has 6 fingers to form separately North Poles and South Poles (Fig. 14.17).
The magnet excitation winding is wound around a soft-iron core. Two carbon brushes rub on two copper slip rings, and make contact with the windings. Two types of brush arrangement in use are ;
(a) Cylindrical or barrel type in which two slip rings are placed side-by-side.
(6) Face type in which the two brushes are fitted coaxially with the shaft.
The rotor is driven by the crankshaft through a vee-belt-pulley and Woodruff-type key. Since alternators are operated for speeds up to 15,000 rpm, and because the belt tension must be sufficient to prevent slip at this high speed, the rotor is supported on ball bearings. These bearings are lubricated and sealed for its life period. A centrifugal fan fitted adjacent to the pulley circulates air through the machine to cool the semiconductor devices used in the system and to prevent overheating of the windings.
Fig. 14.17. Rotor construction.
Stator. The stator is a laminated soft-iron member attached rigidly to the casing which carries three sets of stator windings (Fig. 14.18). The coils of comparatively heavy-gauge enamelled copper wire form the stator windings and are arranged so that separate AC waveforms are induced in each winding when cut by the changing magnetic flux. The two ways in which the three sets of windings can be interconnected are (i) Star and (ii) Delta.
Fig. 14.18. Stator construction.<
Fig. 14.19. Stator windings.
Both types of stator windings are shown in Fig. 14.19. In the Star arrangements, one end of the three windings is connected together and the output current is supplied from the ends A, B and C. In the Delta arrangement the three windings are connected in the form of the Greek letter ‘A’ and the output is again taken from points A, B and C.
The main difference between the two connections is in the magnitude of the output. In the Star arrangement the voltage between any two output points is the sum of the emf induced in two associated windings, whereas the voltage from the Delta arrangement is limited to the emf induced in a single winding only. For a given speed and flux density,
Voltage output from star winding = 1.732 x voltage output from Delta winding.
The output from the Star arrangement is obtained mainly from two windings, but the total is not doubled. It is because only one winding can be positioned at any one time at the point of maximum magnetic flux, hence the value 1.732 i.e. V3~. The energy generated for both arrangements at a given speed is equal, and hence a comparison of current outputs gives,
Current output from Delta winding = 1.732 x current output from Star winding.
The majority of the alternators for light-cars use the star windings, but the Delta wound stator is preferred for higher current output. On some special designs of heavy-duty alternators, the stator windings can be altered from Star to Delta when a large output current is needed.
14.8.3.
Current Rectification
For rectification of the generated current, some alternators install an external plate-type selenium rectifier, but most units use semiconductor diodes, arranged to form a bridge network. With a 3-phase output, 6 diodes are arranged as shown in Fig. 14.20 to give full wave rectification. Since the diodes act as one-way valve, the current generated in any winding always flows to the battery through the terminal B+. A complete circuit is required for the flow of this direct current, therefore an appropriate earth diode (the negative diode in this case) is used to pass current from ‘earth’ to the active winding.
In addition to current rectification, the diodes do not allow flow of current from the battery when the alternator output voltage is less than the battery voltage. Therefore the diodes eliminate the use of a cut-out as is necessary in a dynamo charging system. With the alternator
stationary, the connection to the alternator B+ is ‘live’. This must be remembered while demounting an alternator from the engine. The battery earth terminal should be disconnected prior to initiating work on the alternator.
Figure 14.21 illustrates various options adapted to mount the rectifier diodes. However, in all constructions the semiconductors must be kept cool, so it is common to mount the diodes on a heat sink made of an aluminium alloy block or plate.
14.8.4.
In addition to current rectification, the diodes do not allow flow of current from the battery when the alternator output voltage is less than the battery voltage. Therefore the diodes eliminate the use of a cut-out as is necessary in a dynamo charging system. With the alternator
stationary, the connection to the alternator B+ is ‘live’. This must be remembered while demounting an alternator from the engine. The battery earth terminal should be disconnected prior to initiating work on the alternator.
Figure 14.21 illustrates various options adapted to mount the rectifier diodes. However, in all constructions the semiconductors must be kept cool, so it is common to mount the diodes on a heat sink made of an aluminium alloy block or plate.
14.8.4.
Field Excitation
Unlike the dynamo, insufficient residual magnetism is present in the magnetic poles to initiate the charging process, hence a battery initially excites (activates) the field magnets. Early alternators incorporated a field relay to connect the battery to the field when the ignition is switched-on. Presently a self-excited system with three field diodes is used to supply the rotor field with a portion of the current generated by the
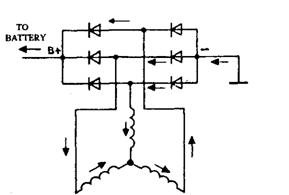
Fig. 14.20. Rectifier circuit.

Fig. 14.20. Rectifier circuit.
No comments:
Post a Comment